In this paper, we explore how ROM can be leveraged to perform a non-invasive attack (i.e., voltage glitching) by a relatively unsophisticated actor without a six-figure budget. We begin by explaining what ROM is, why it is used, and how it can be extracted.
What exactly is ROM?
Put simply, Read-Only Memory (ROM) is a type of Non-Volatile Memory (NVM) that is constructed as physical structures within chips. The structures are patterned as ones and zeroes on one, and only one, of several layers of the chip. Why just one? Cost. ROM is real hardware, and making any hardware changes in the layout of a chip is very expensive.
The fact that ROM is physically encoded in a chip makes it uniquely reliable and thus appropriate for critical functions, such as boot code execution. ROM is infinitely more reliable than NVM that relies on an electrical charge, like Flash.
The following table provides a brief overview of memory classes.

How can you extract data from ROM?
If there is no protection on the device (i.e., it is embedded on a development board), then it is simple to access the data and dump it as a binary (.bin) file. By doing so, we have essentially extracted the final code, as opposed to the raw bits. This means that the code is in an understandable format (no need to decrypt or descramble) and can be analyzed using standard software reverse engineering tools, like IDA Pro or Binary Ninja, to isolate a weakness in the bootloader.
If the ROM is protected, then there is the option to physically deprocess sample chips (more on that later) and extract the raw bits as ones and zeroes. The process is very skill dependent; however, it is possible to carry out on a shoestring budget depending on the age of the chip technology. In some cases, only a polishing wheel, a handheld polishing jig, and an optical microscope are needed.
Reading out the raw bits is only the first step of the process, as these bits need to be further analyzed and manipulated to properly understand the code. The complexity of reverse engineering will vary depending on the following:
Is the ROM scrambled?
Scrambling is when the data is ‘mixed-up’ at the periphery of the memory block. In this case, it is enough to study the peripheral circuitry to make sense of the data.
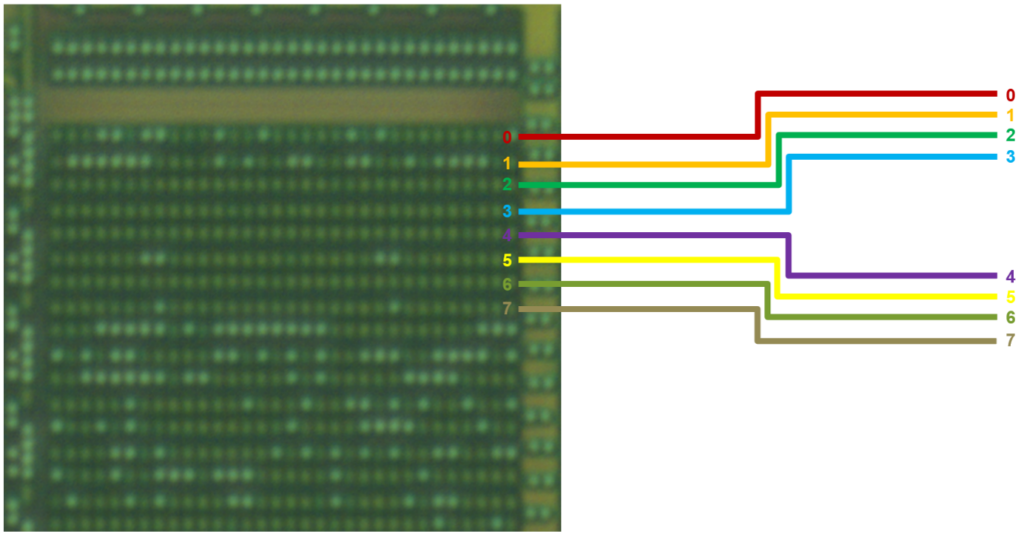
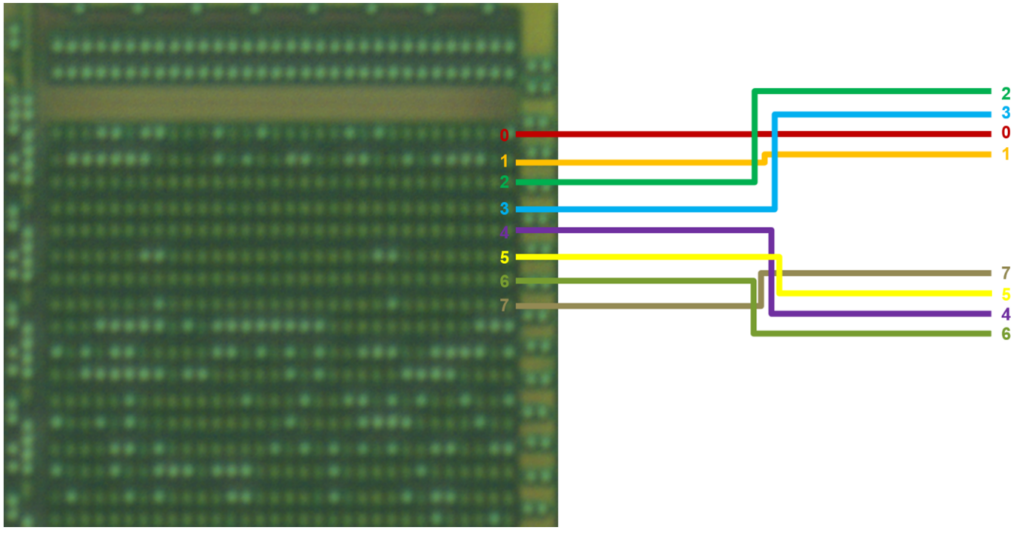
The ordering may also vary byte-to-byte, making reverse engineering more difficult.
Is the ROM encrypted?
Encryption is far more difficult to reverse engineer because the data is routed out of the memory and into the CPU logic, which is usually vast and, on its face, random. The data will be routed to the decryption circuitry, which may only be a few dozen logic cells.
Finding the decryption circuitry in a sea of one hundred thousand logic cells with no direction on where to start is an extremely difficult task. It may be necessary to reverse engineer the entire CPU logic; however, there are isolation techniques like thermal or photon emission that can help identify a specific area of interest on the chip. Using such techniques, the chip is instructed to repeatedly decrypt data while the entire chip is monitored for heat or light emissions, revealing the area of the chip that is performing the decryption. This smaller area of the chip then becomes the focus of reverse engineering.
Is the ROM both scrambled and encrypted?
If the ROM is both scrambled and encrypted, recovering the data will require analysis of the addressing logic and reverse engineering some if not all of the CPU logic. If the raw data is encrypted, the physical bit pattern will look the same, whether it is scrambled or not.
How do you deprocess a chip?
Deprocessing is the physical removal of layers from a finished chip using chemical and mechanical techniques. The process is necessarily destructive and can be used to remove one or more layers, depending on the target.
Consider the following example chip:
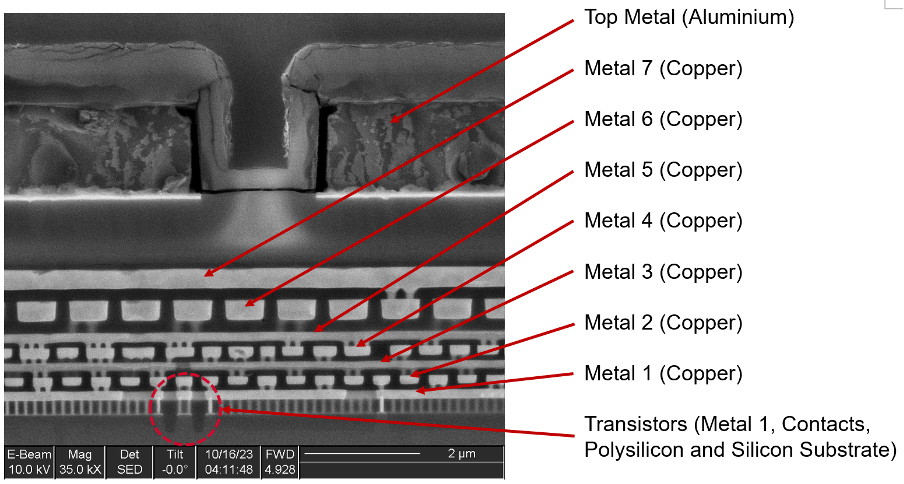
We can see that the chip is constructed of many layers of copper circuitry, all embedded in an insulator (glass-type material). Transistors are literally the building blocks of digital components and are fabricated on the silicon substrate at the bottom of the chip. Therefore, the ROM transistors will be located on the bottom as well. The raw bits we are looking for (the ROM encoding layer) will likely be at the Contact, Metal 1, or Via 1 layer (between Metal 1 and Metal 2), but we won’t know for sure until we start destroying some chips.
If we have the time and sufficient samples, we can start by removing all of the layers from one chip in order to analyze the floorplan. Based on this analysis, we can map out where the memories are located and even identify what types of memories are present, such as Flash, SRAM, DRAM, or ROM. This will help identify the specific area of the chip to focus on when attempting to extract the raw bits. In addition, we could also cross-section a chip at the location of the ROM to help determine which layer contains the bit encoding to guide our work.
If we don’t have the time or the samples, we can just go ahead and carefully deprocess a single chip, and at some point, the ROM bits will appear. But if we deprocess too far, we will go past the bit encoding layer and lose the data.
For our work, we will use the most basic and fastest technique—mechanical polishing. While many argue that mechanical polishing is the most effective method for deprocessing chips, it is also the most skill dependent.
We can polish in several ways (in order of increasing sophistication and cost):
- Manual finger polishing: The decapsulated chip is placed on the fingertip and polished on a static plate or piece of glass.
- Turntable finger polishing: Similar to manual but uses a rotating platen to expedite the polishing process (and eliminate Repetitive Strain Injury!).
- Manual polishing with fixture (jig): Uses a rotating platen in conjunction with a polishing fixture that can be adjusted to compensate for non-planarity.
- Semi-automated polishing: Uses a purpose-built system with control over:
- Platen speed
- Sample planarity
- Force applied to sample
- Sample rotation (in addition to platen rotation)
In this example we used the third approach because a turntable accelerates progress, and a polishing jig offers fine angle control. Additionally, the manual polishing table and jig, as well as the abrasives involved, are relatively low-cost items, keeping the approach within reach of a skilled and motivated hobbyist.
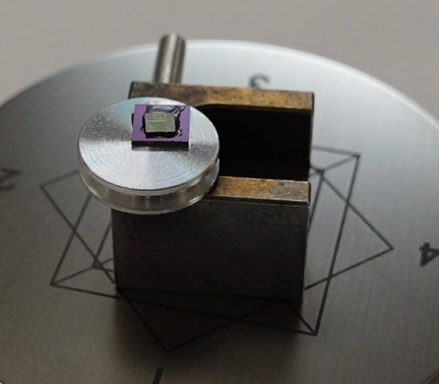
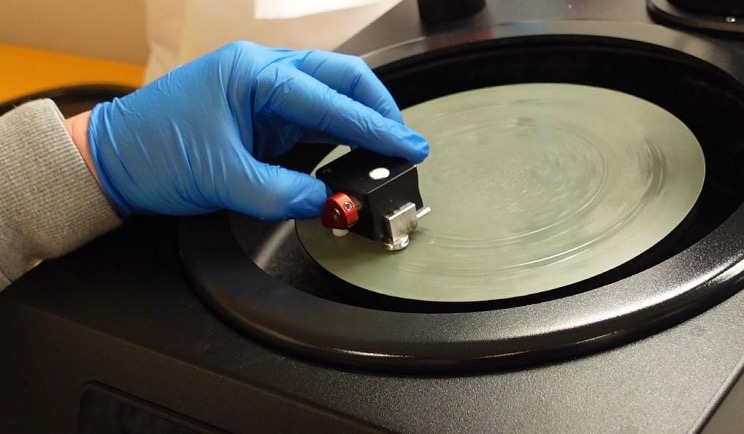
Determining when to stop polishing (end pointing) is difficult; however, when we hit the ROM encoding layer, we should see some kind of pattern under an optical microscope, even at 5x magnification.
The image below was taken at 20x magnification, and we can categorically say that we have reached the right layer.
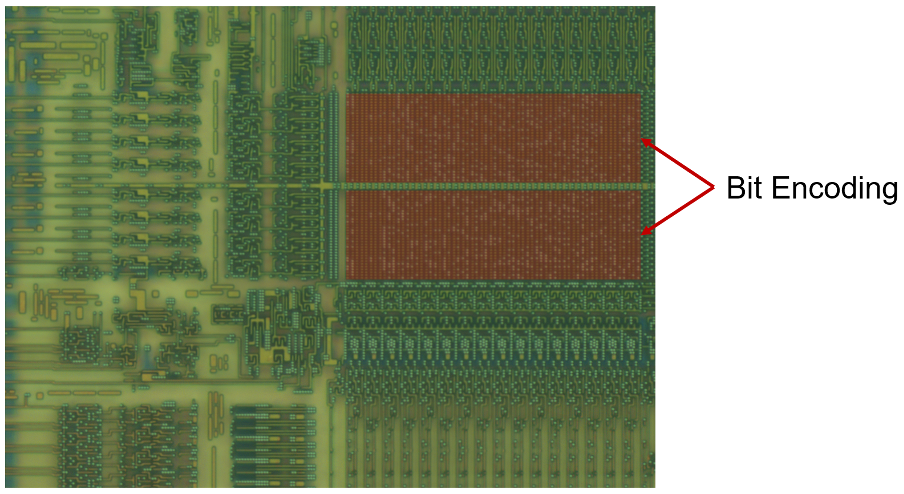
The bits appear as white dots from above, because they are bullet-shaped Tungsten interconnects, a little like the contacts shown in the following cross-section images:
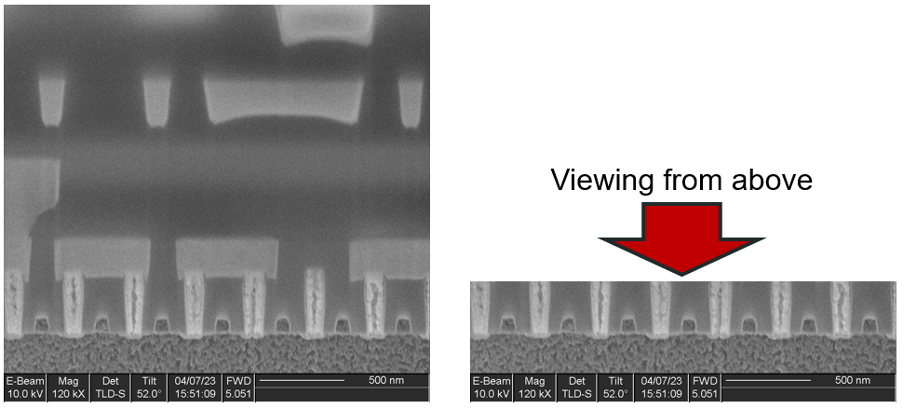
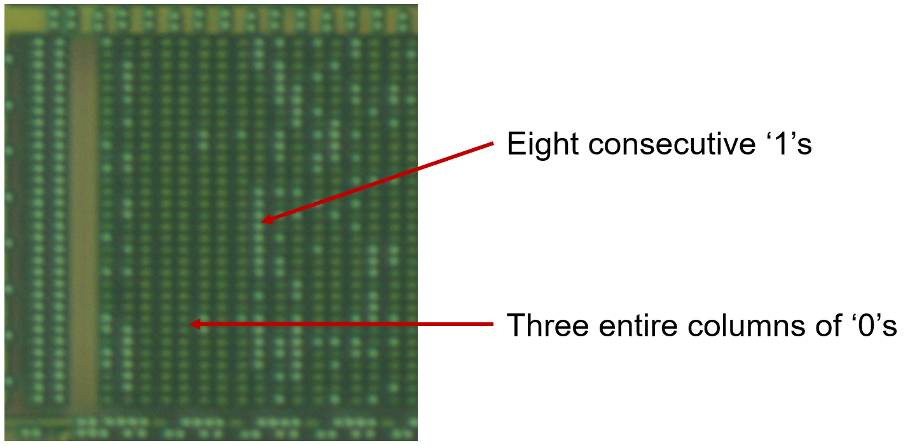
We can see from a very high-level visual inspection that the ROM cannot possibly be encrypted, due to the distribution of ones versus zeroes. If the data was properly encrypted, then the distribution would appear random; however, a visual assessment is sufficient to confirm a lack of entropy without the need to formally calculate[1] it with binwalk[2] or another tool. We can conclude that although the data may be scrambled, it is not encrypted. There is enough evidence to tell us that if we extract the raw bits, we can derive the addressing to then get us back to an understandable binary.
For now, we don’t need to carefully analyze the addressing circuit; all we need is to determine if there is any scrambling in the addressing logic. We can do this visually.
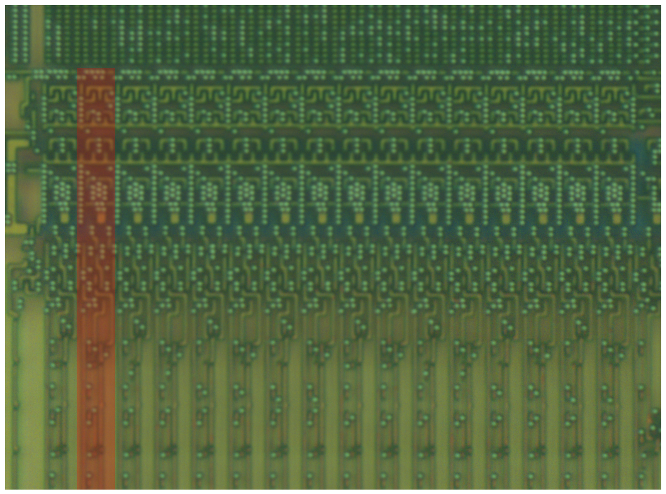
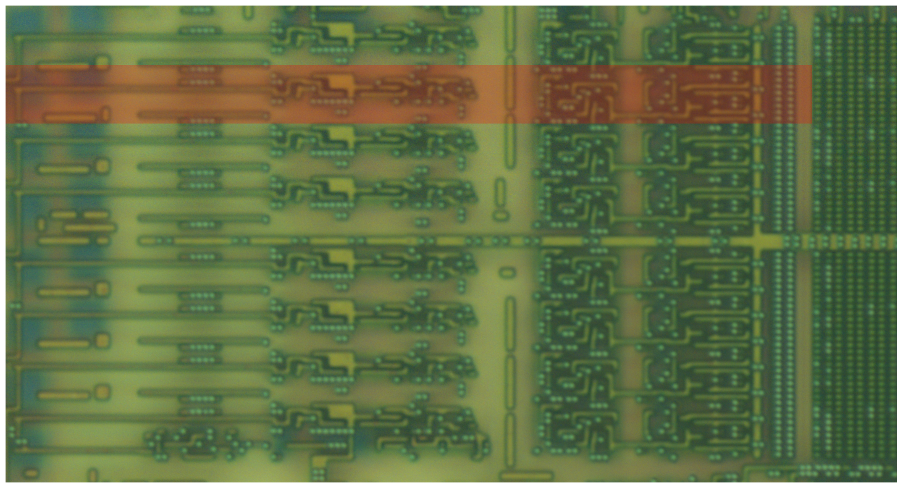
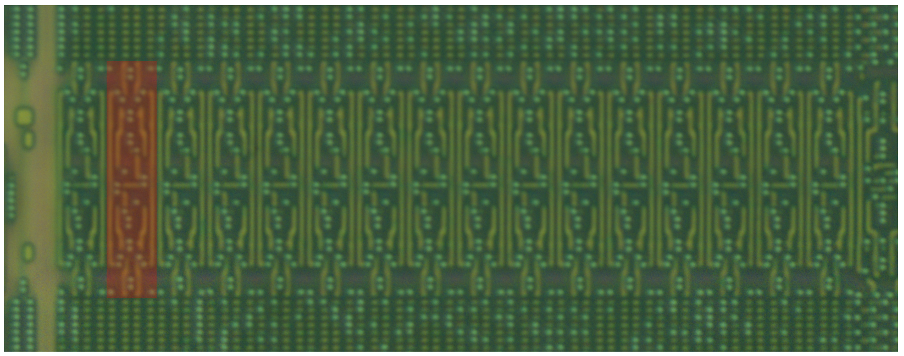
When we isolate a small area of the decoding/addressing circuitry at any point (bottom, left, or between the blocks), it is perfectly repeated. This proves that the ROM is not scrambled, and all we need to do is to work out how the bits are read to recreate the full binary. That, and extract the raw bits, of course.
No Scrambling 😊
No Encryption 😊
How do you extract the raw bits?
It is preferable that we automate the extraction process, as the ROM’s capacity is 16 KB (128,000 single bits), which is far too much to extract manually. First, we must determine if our optical images are good enough to reliably extract the raw bits. If not, we may need to use a Scanning Electron Microscope (SEM) to obtain higher resolution, higher contrast images.
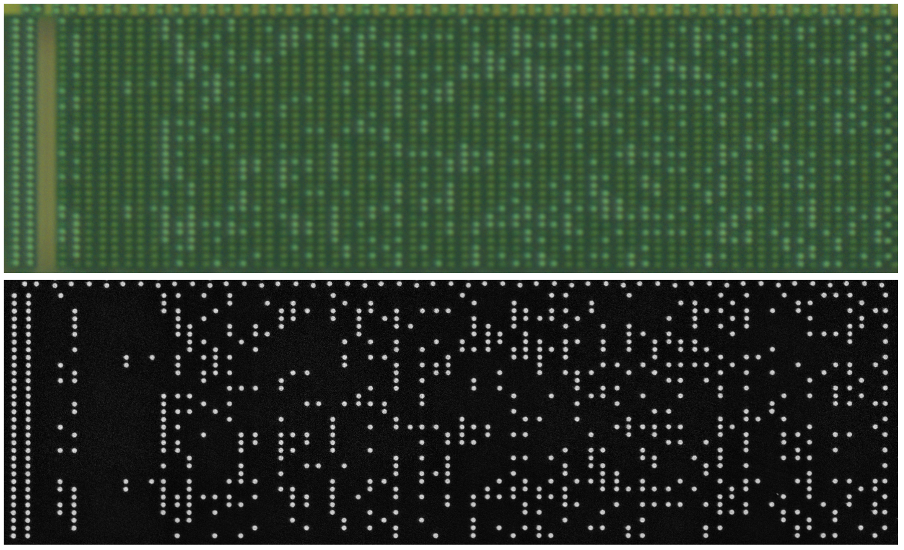
Clearly there is a huge difference in resolution and, more importantly, contrast between the two types of images. It’s obvious that using SEM images would expedite the extraction process, but let’s see if we can use the optical images and do this on a shoestring budget.
First, we need to optimize the optical test image with photo editing software to maximize our chances of success. A good start is always to use the filters in Photoshop such as ‘Noise – Despeckle’ and ‘Noise – Dust and Scratches.’ The final step would be to manipulate the levels to maximize the contrast.
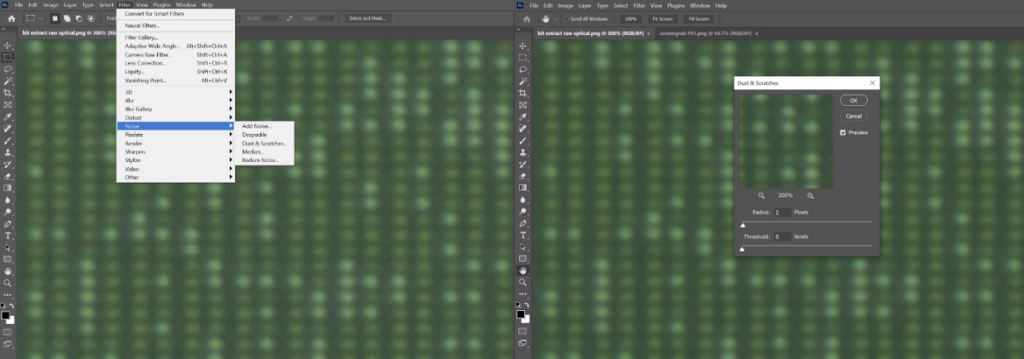
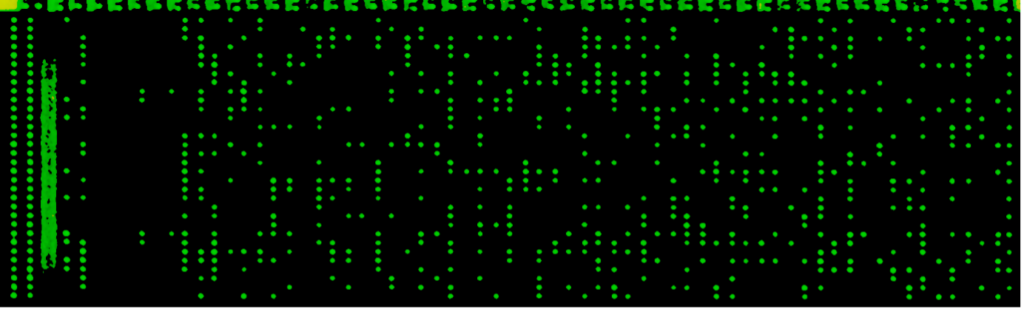
Perhaps quite surprisingly, simply by filtering and adjusting the levels of the optical image, we can almost end up with the same result as with the SEM.
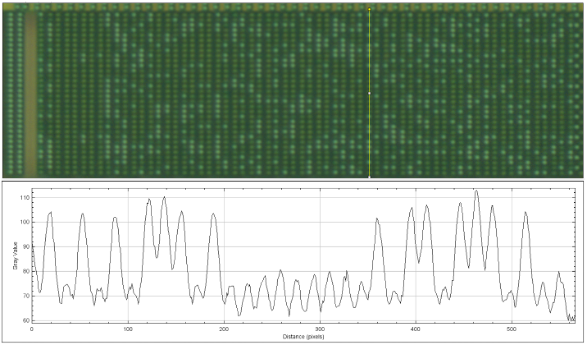
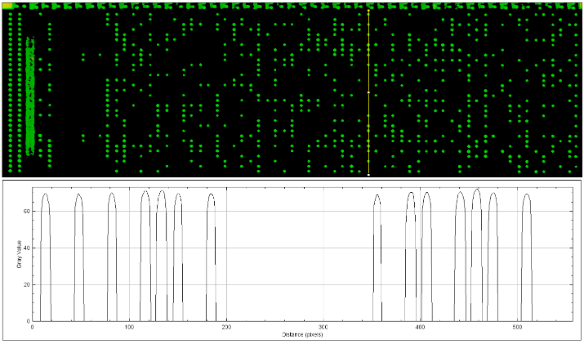
From this simple test, we can conclude that any effective tool will be capable of reliably extracting the raw bits from our optical images.
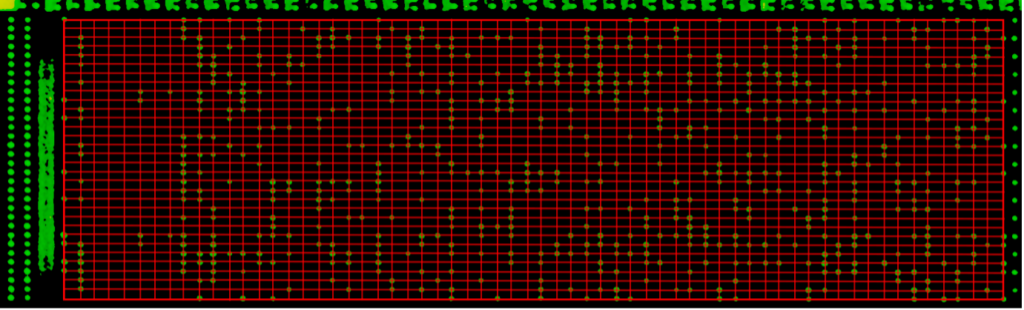
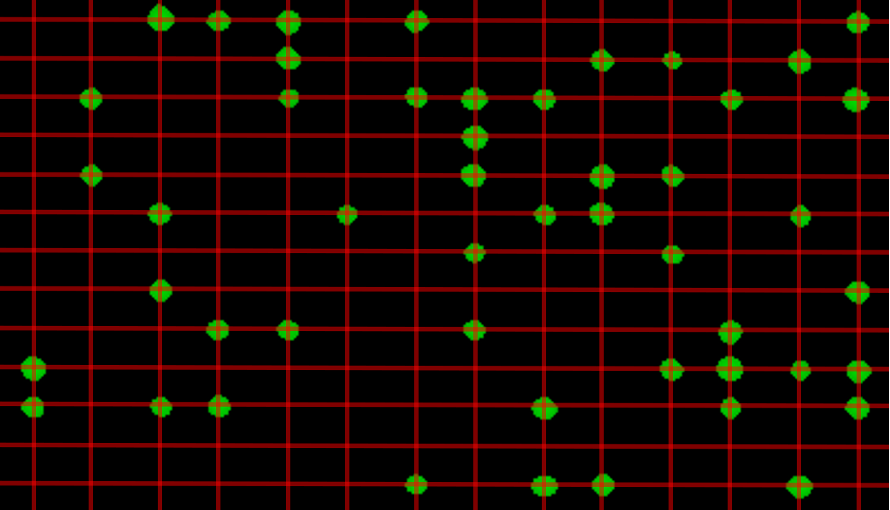
Commercial software is available for semi-automated ROM bit extraction. The software measures the brightness of the area around the line intersections and compares that against a user-defined estimate for both a one and a zero. The software then assigns values to each area in which a bit exists, then exports the values to a text file. Below is the text extracted from this small piece of ROM. This is a fraction of one of 64 sections within the memory array, so some time is required for a full extraction. There is certainly an AI/ML opportunity here to expedite the process.

After repeating the process many times, we have the entire ROM in our hands, and we can move onto the next step: deriving how the bits are addressed. At this point, we will have a usable binary to work with in IDA Pro or Binary Ninja so we can understand the boot process and find some potential areas of weakness we can glitch.
Bits to Binary
As this is a chip with a known vulnerability, it was possible to dump the entire ROM via JTAG. We will use this dump to help us do two things:
- Deduce how the ROM is addressed
- Compare our physically extracted ROM with the JTAG dump to validate our process
To illustrate the analysis of our physically extracted dump, we will use the higher-resolution SEM images we acquired after the optical images were taken.
Let’s start by looking at the electrical dump of the ROM. The following output is the beginning and end of the ROM .bin, with the end looking very much like a checksum. We know this is commonly used by this manufacturer, so after many zero bytes, there are two bytes of data at the very end of the file.
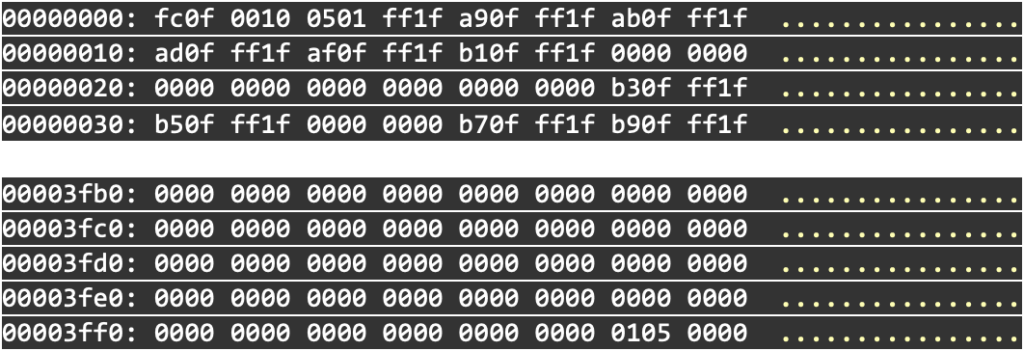
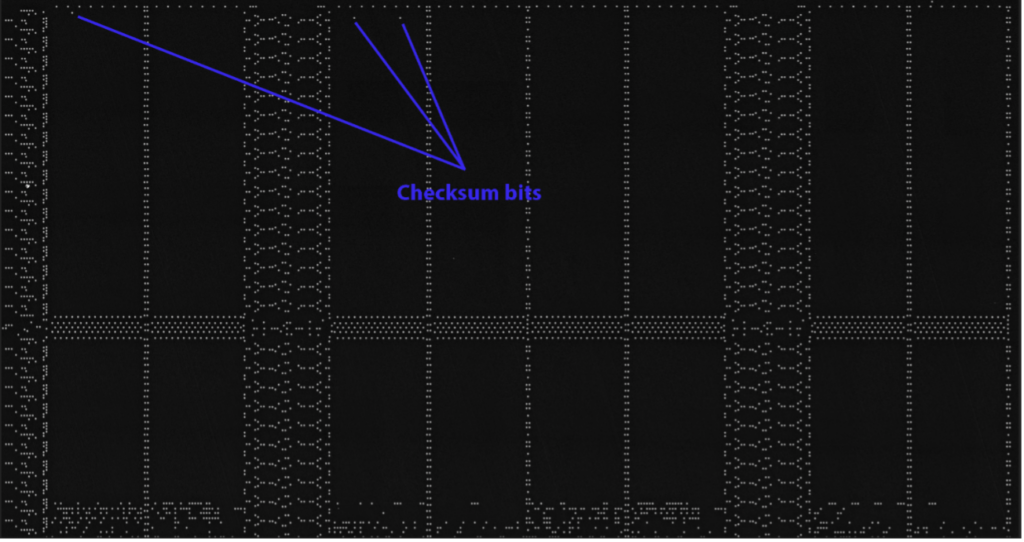
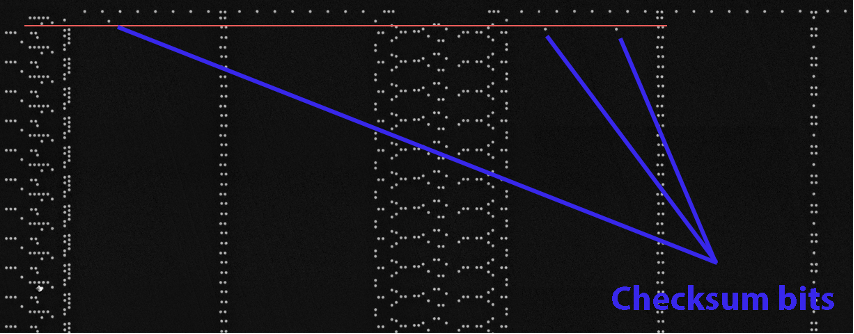
From the fact that we have the two-byte checksum (0105) in hex, and that the corresponding raw bits (0000 0001 0000 0101) are not in a linear pattern, then we must assume that there is some flipping/mirroring happening on the bit addressing. The fact that the bits are split over two rows also gives us a clue.
Now our checksum is beginning to make sense. With a checksum of 0105 (0000 0001 0000 0101), there must only be one way to read it. Essentially, we are looking for how the three ones are addressed.
First, we can see that the three bits are all on the same bit column, so we can ignore the rest. It makes things easier to visualize by annotating all of the bit columns, then highlighting the only column (column 0) we care about in yellow. The values are now much easier to read by eye, and we can see the direction in which they are read by the memory array.
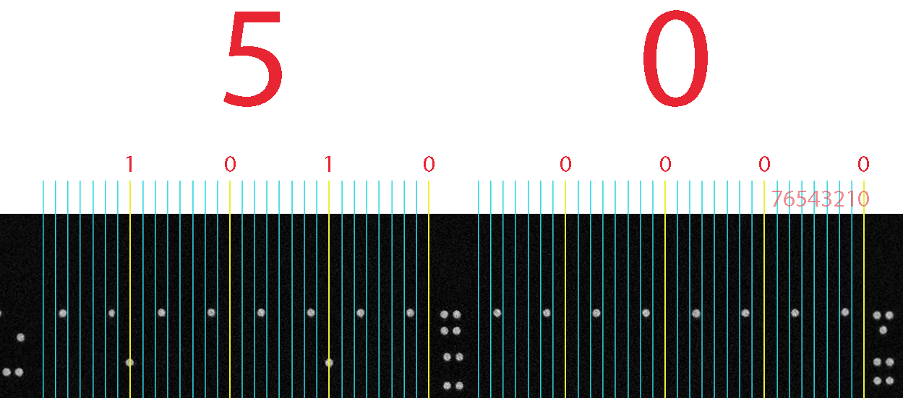
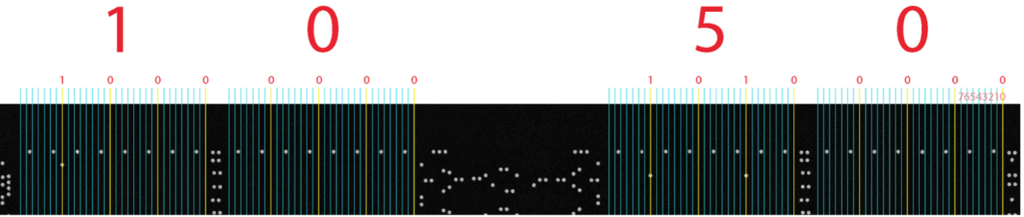
We now see that 0105, albeit not in a logical order for a human. There is one question mark remaining: Do we assume that we read the left side in reverse first (01) followed by the second (05)? There we have a simple 50% chance of being correct, and to find out, we can apply that to the more densely populated areas of ROM.
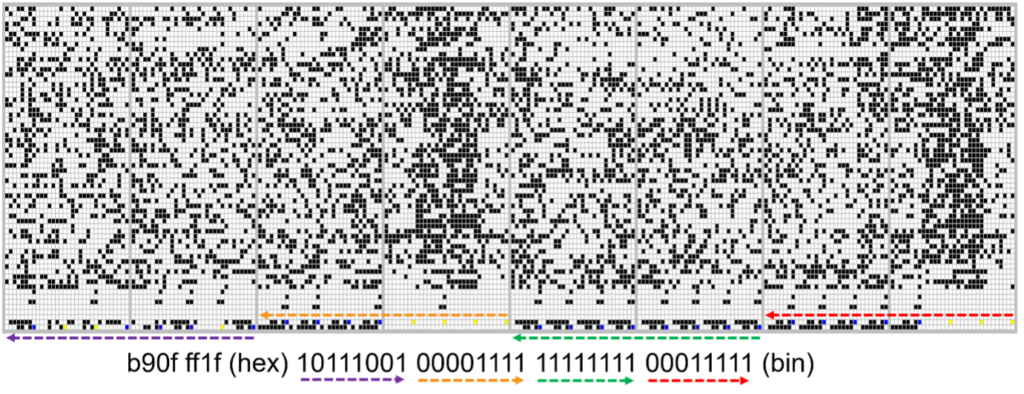
The portion of ROM above shows the hex value along with the raw binary for the two-word width of the ROM array. The colored arrows illustrate the direction in which the bits are read from the .bin and how they are read from the raw bit image. The following is a closer view of one byte, where blue bits are logical ones and yellows are logical zeros:
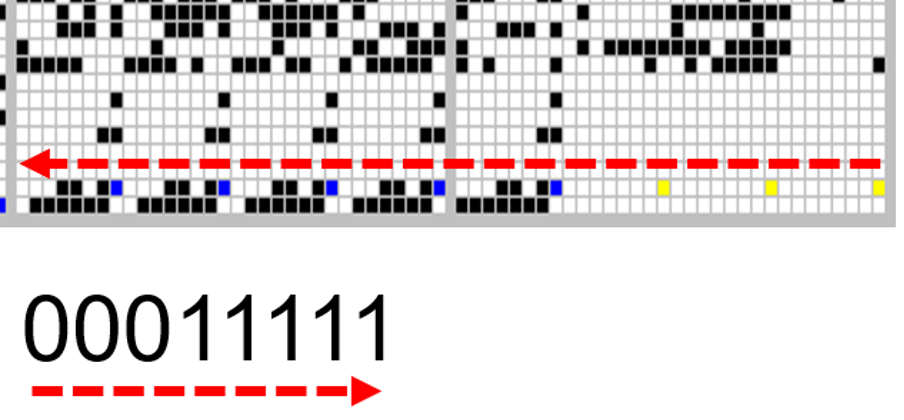
Finally, a binary!!!
The following image contains some dumped bytes from the target. This can be later be opened in the reversing tool of our choice, and after some preparation work, we can begin reverse engineering and identifying the potential weaknesses. In this case, as some readers might know, the target sample has a known vulnerability that can be exploited via fault injection. This vulnerability can allow an attacker with physical access to the device to retrieve the entire contents, even if the chip has been locked down.

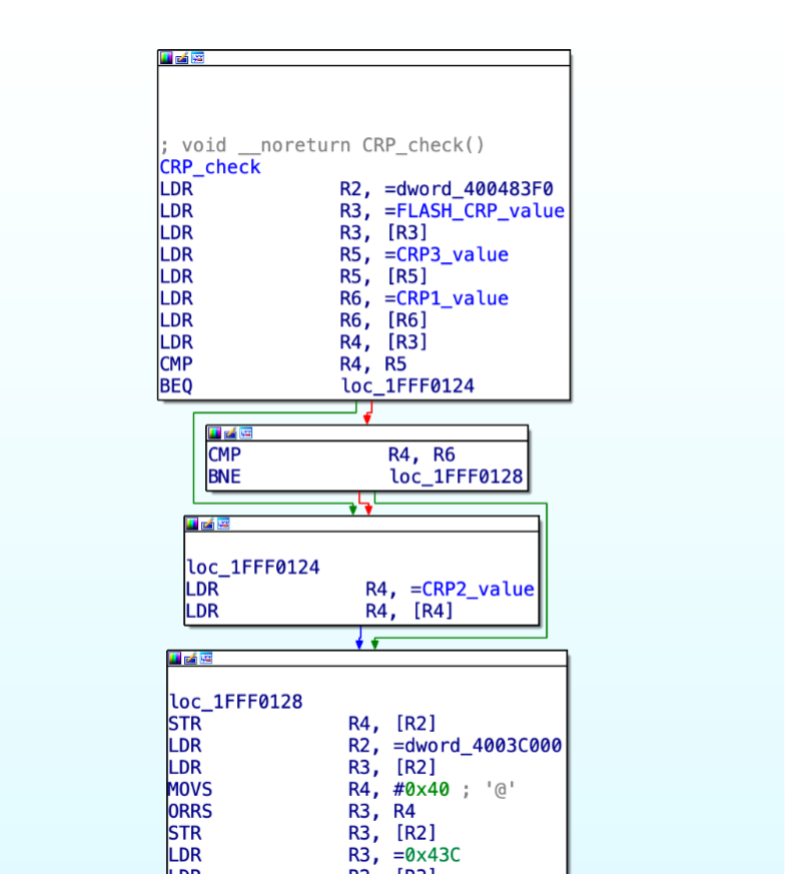
Overall Conclusions
- While a chip with a known vulnerability was used in this case study for comparative purposes, the same techniques can be applied to a chip without this vulnerability
- The electrical version of the ROM dump matched 100% with the physically extracted version
- Physical ROM bit extraction is skill-dependent, but can be carried out using a relatively basic toolset such as:
- Basic polishing turntable
- Handheld polishing jig
- Diamond abrasives
- Optical microscope
- ROM binary extraction is dependent on:
- Existence of encryption
- Complexity of scrambling
- Patience!
- ROM binary analysis and isolation of glitching/fault injection points is possible
- Electrical and electromagnetic fault injection techniques are skill- and chip-dependent; however, the bar of entry is relatively low (hundreds to thousands of dollars)
[1] https://resources.infosecinstitute.com/topics/cryptography/entropy-calculations/
[2] https://github.com/ReFirmLabs/binwalk